The manufacturing industry has undergone massive changes in recent years, with technology playing a pivotal role in reshaping how businesses operate. Yet, many factories still cling to traditional methods, unaware of the hidden costs of ignoring transformative technologies like the Internet of Things (IoT). IoT for manufacturing industry is no longer a buzzword; it’s the game-changer driving efficiency, reducing costs, and unlocking new opportunities for growth. If your business hasn’t embraced this revolution, it might already be lagging behind.
Let’s dive into why ignoring IoT could be costing your manufacturing business more than you realise—and how adopting it can save the day.
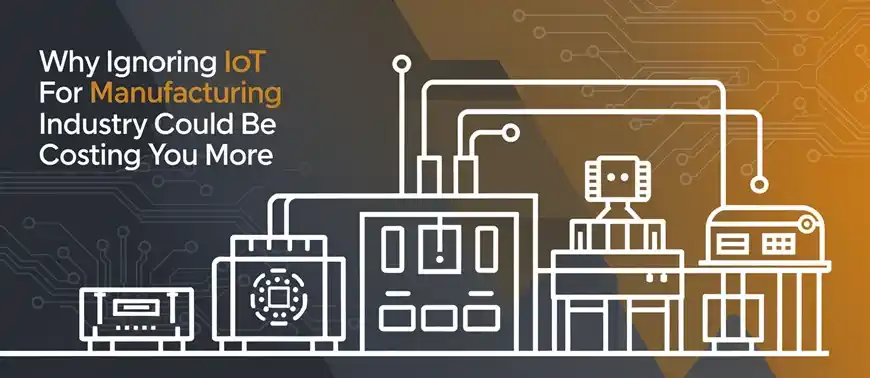
1. Rising Downtime and Maintenance Costs
How often do unexpected breakdowns disrupt your production schedule? Downtime is one of the most significant hidden expenses for manufacturers, often leading to lost revenue and missed deadlines. Without industrial IoT solutions for smart manufacturing, you’re essentially running blind when it comes to machine health.
IoT-enabled sensors can monitor equipment in real-time, detecting signs of wear and tear long before they lead to costly failures. Predictive maintenance powered by IoT ensures that you’re not only avoiding downtime but also extending the lifespan of your equipment. Can you really afford to overlook such a crucial solution?
2. Poor Supply Chain Visibility
In the fast-paced manufacturing world, delays in the supply chain can ripple through operations, creating bottlenecks and inefficiencies. Traditional systems often fail to provide real-time visibility, leaving manufacturers playing catch-up. With IoT solutions for manufacturing, you can achieve end-to-end visibility across your supply chain. IoT-enabled RFID tags and sensors track shipments, inventory, and raw materials in real-time, ensuring you’re always one step ahead. Ignoring IoT means continuing to suffer from delays, inaccuracies, and waste—issues that could easily be resolved with the right technology.
3. Missed Opportunities for Energy Optimisation
Manufacturing plants are among the largest energy consumers in any economy. Already, surging energy prices are shaving off much-needed profit from operations, but wasted energy compounds this loss. Through IoT, manufacturing firms can monitor and optimise their energy use and determine exactly where to trim unnecessary energy spending. Ignoring IoT means missing out on these savings, making your factory vulnerable to rising utility costs. Even worse, it may also tarnish your reputation, as more consumers and partners prefer companies that focus on sustainability.
4. Inconsistent Product Quality
In manufacturing, quality is paramount. However, without the most advanced tools, it can be difficult to achieve consistency in high-volume production. Manual quality control checks are liable to errors, defects, and wastage of resources. IoT-enabled sensors and cameras make automated quality control a reality. These systems detect defects in real-time, ensuring every product meets the required standards. By ignoring IoT for manufacturing industry, you risk delivering inconsistent products—something no business can afford in today’s competitive market.
5. Data Silos Preventing Smarter Decisions
Data is the backbone of modern manufacturing, but most businesses do not use it effectively. In the absence of IoT, data remains confined to individual departments and does not provide the overall big-picture insights that drive smarter decisions. IoT integrates data from across your factory, giving you real-time analytics on production rates, bottlenecks, and performance. These insights empower managers to optimise workflows and respond instantly to changing demands. Without IoT consulting, you’re essentially leaving money on the table by not utilising your data to its fullest potential.
6. Falling Behind Competitors
The manufacturing landscape is more competitive than ever. Businesses embracing IoT are pulling ahead, thanks to increased efficiency, reduced costs, and faster turnaround times. Ignoring IoT means risking obsolescence, as competitors who adopt this technology gain a significant edge.
For instance, autonomous robots powered by IoT are revolutionising tasks such as material handling, assembly, and quality checks. These advancements reduce labour costs and increase production speed, leaving traditional factories struggling to keep up.
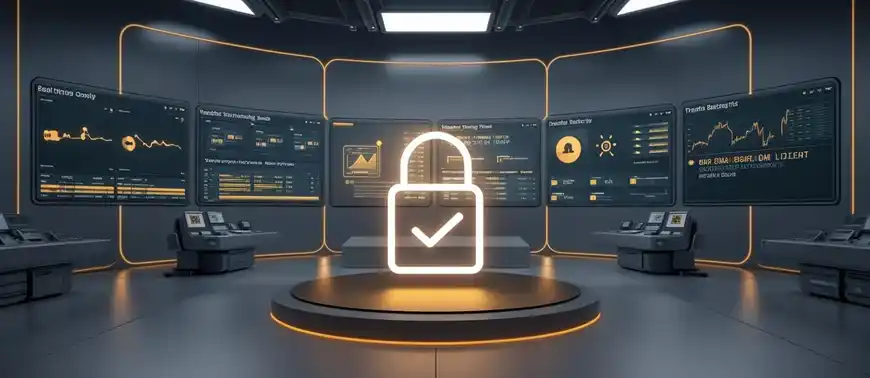
7. Poor Scalability
As your business grows, the management of operations becomes increasingly complex. Most traditional systems struggle to scale, and this creates more operational pain in terms of increased cost. IoT offers the flexibility needed to scale seamlessly. Cloud-based platforms and IoT-enabled devices ensure your factory can handle increased demand without missing a beat. Ignoring this potential means hampering your growth and risking inefficiencies as you expand.
8. Increased Security Risks
Cybersecurity is a growing concern in the manufacturing industry, particularly as operations become more connected. Ignoring IoT could leave you vulnerable to cyberattacks, as traditional systems lack the advanced security features of IoT-enabled platforms. IoT solutions come equipped with robust security protocols, including real-time monitoring and biometric authentication. These measures protect your operations from threats, ensuring business continuity and customer trust.
Why Now is the Time to Act
The manufacturing industry is at a tipping point. The technologies that once seemed futuristic—like IoT, AI, and robotics—are now essential tools for success. To look away from implementing IoT in a manufacturing industry puts your business up for more high costs and ineffectiveness compared to its competitors. Adopting IoT isn’t just about keeping up; it’s about staying ahead. From predictive maintenance to automated quality control, IoT offers solutions that address the most pressing challenges in manufacturing today.
Taking the First Step: IoT Consulting for Manufacturing
If you’re unsure where to begin, IoT consulting for manufacturing can guide your journey. Consultants help assess your current systems, identify improvement areas, and help develop specific strategies suited to integrating IoT into your business. This means achieving maximum ROI while focusing on your specific pain points.
The Bigger Picture: Embracing Industrial IoT Solutions for Smart Manufacturing
By adopting Industrial IoT solutions for manufacturing, you’re not just investing in technology; you’re investing in the future of your business. These solutions enable smarter decision-making, improve operational efficiency, and pave the way for sustainable growth.
Conclusion
The cost of ignoring IoT is far greater than the initial investment required to implement it. From lost revenue due to downtime and inefficiencies to falling behind competitors, the risks are too significant to overlook. By embracing IoT for manufacturing industry, you can unlock unprecedented levels of efficiency, productivity, and innovation. The question is no longer whether you can afford to adopt IoT—it’s whether you can afford not to.